Pilots need carefully constructed paths to navigate through our nation's airspace. Creating those paths is complicated and time-consuming. MITRE-developed automation now supports most of them—greatly reducing FAA design time.
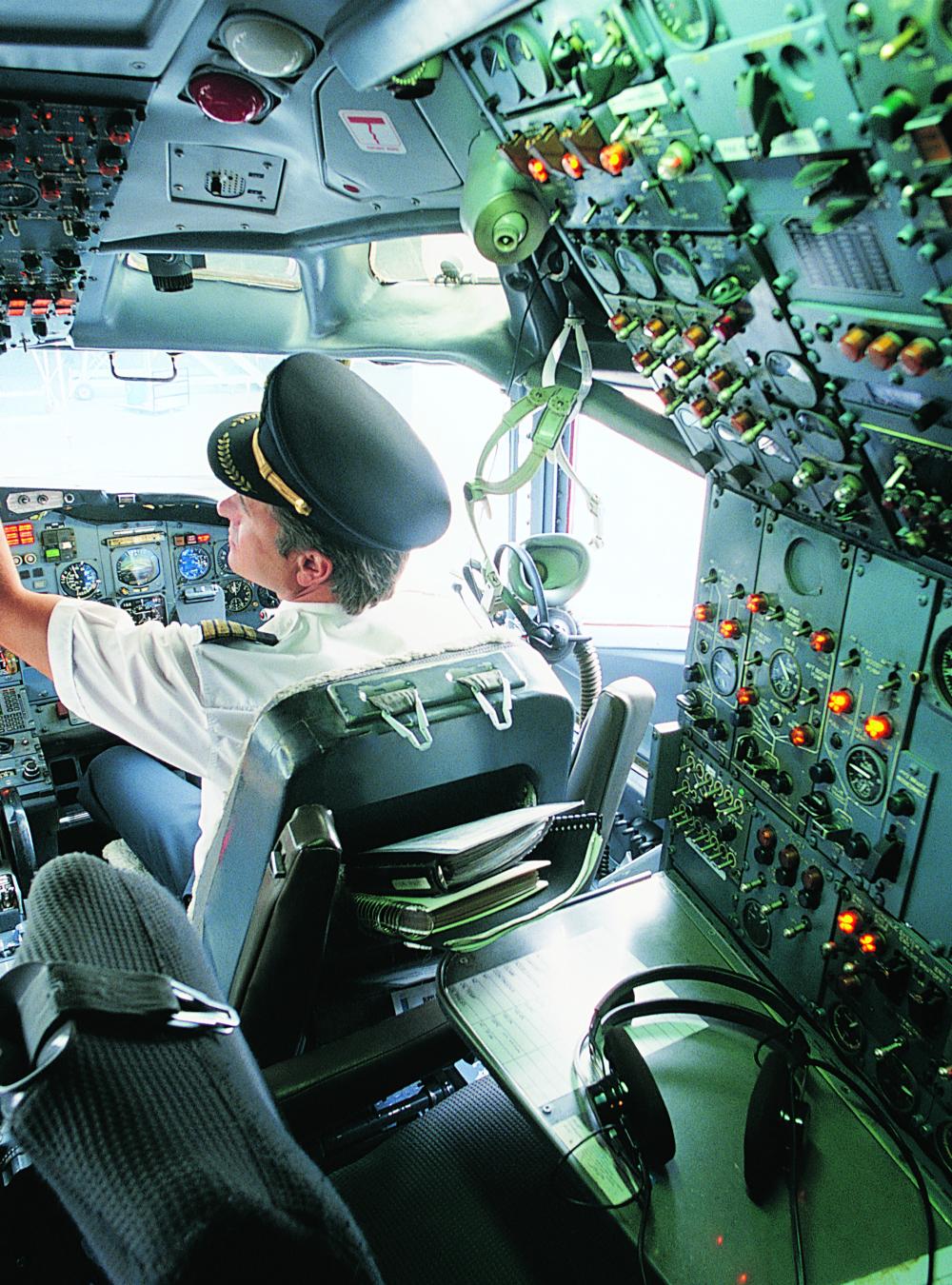
Automation Helps Create Safe Pathways in the Sky
A pilot prepares to fly through busy airspace. Another pilot encounters fog obscuring the out-the-window view. A third pilot wants to safely avoid mountainous terrain. These pilots all need preconceived routes to fly that ensure their aircraft avoid nearby terrain, man-made structures, and other aircraft.
Fortunately, the Federal Aviation Administration (FAA) has nearly 20,000 carefully delineated procedures to accommodate such situations. They are known as instrument flight procedures (IFPs).
But creating and maintaining these procedures is complex and time-consuming, and demand for new IFPs is increasing as aviation technology advances. To streamline the process, the FAA sought the help of MITRE, which operates the FAA's federally funded research and development center.
Now, a MITRE-developed capability called TARGETS makes the IFP development process faster, easier, and more standardized—using automation.
As of September 2019, this automation supports 95 percent of the IFPs in the FAA's IFP inventory.
It's Complicated
To create an IFP, the FAA must consider the proposed operation, the obstructions—both natural and man-made—along that proposed path, and the rules dictating how much distance must be maintained between the aircraft and the obstructions to ensure flight safety.
Until recently, the FAA created IFPs using aging automation that did not align with the latest rules and often required time-intensive manual calculations.
TARGETS now automates the vast majority of the IFP evaluations, reducing the need for manual calculations. The capability applies complex math to translate the rules into algorithms that can run safety checks against the proposed procedure path and obstruction data.
"We've nearly eliminated the need for manual calculations," says Ryan Huleatt, who leads MITRE's work on TARGETS.
The new, more automated process begins with the IFP designer entering the proposed procedure into TARGETS.
"The software retrieves the necessary obstruction information and then runs checks, based on the FAA standards, to determine if any of the obstructions will create a potential safety issue with the procedure," Huleatt explains. "The designer is then notified of any issues. With that information, the designer can quickly revise the IFP design, as needed."
Expanding the Use of IFP Automation
Recently, the FAA also began exploring the use of the IFP automation software to help with the maintenance and retirement aspects of the IFP lifecycle.
Because of changing technology and standards and the constant construction of new obstacles, the FAA must review all existing IFPs every two to four years to ensure safety.
"On average, the FAA conducts between 500 and 1,000 of these reviews per month," Huleatt says. "Each takes between half a day and several days to complete. That means the FAA devotes a significant amount of time and effort to this important review process."
MITRE is helping the FAA to streamline the review process. A key focus is to automatically identify IFPs needing review based on new or planned obstructions or rule changes—rather than on a time-based schedule—and run them through the automation to perform safety checks. That will help focus IFP developers' attention on the procedures most needing review or revision.
For example, if a new skyscraper is under construction and its planned dimensions are known, an analysis could be run to determine which IFPs would be affected. Those IFPs could then be flagged for proactive revision.
Additionally, when combined with other data, this automated capability will allow the FAA to regularly scan its inventory for IFPs that may be candidates for retirement.
Looking to the Future
The FAA and MITRE are also researching how artificial intelligence (AI) and machine learning (ML) techniques could assist in IFP development.
Currently, the process relies on the expertise and experience of human IFP designers, who must balance the safety standards and inputs from stakeholders on the operation. AI/ML techniques could assist the designer in optimizing for different constraints and objectives. And that could greatly reduce the number of design iterations required to create a new IFP.
"That would produce even more time and cost savings for the FAA," Huleatt says. "We're working with the FAA to make that a reality."
—by Marlis McCollum