As demand for face shields and other personal protective equipment grew, the University of Virginia searched for ways to safeguard providers. MITRE collaborated with the university to provide a new 3D-printed shield in just two weeks.
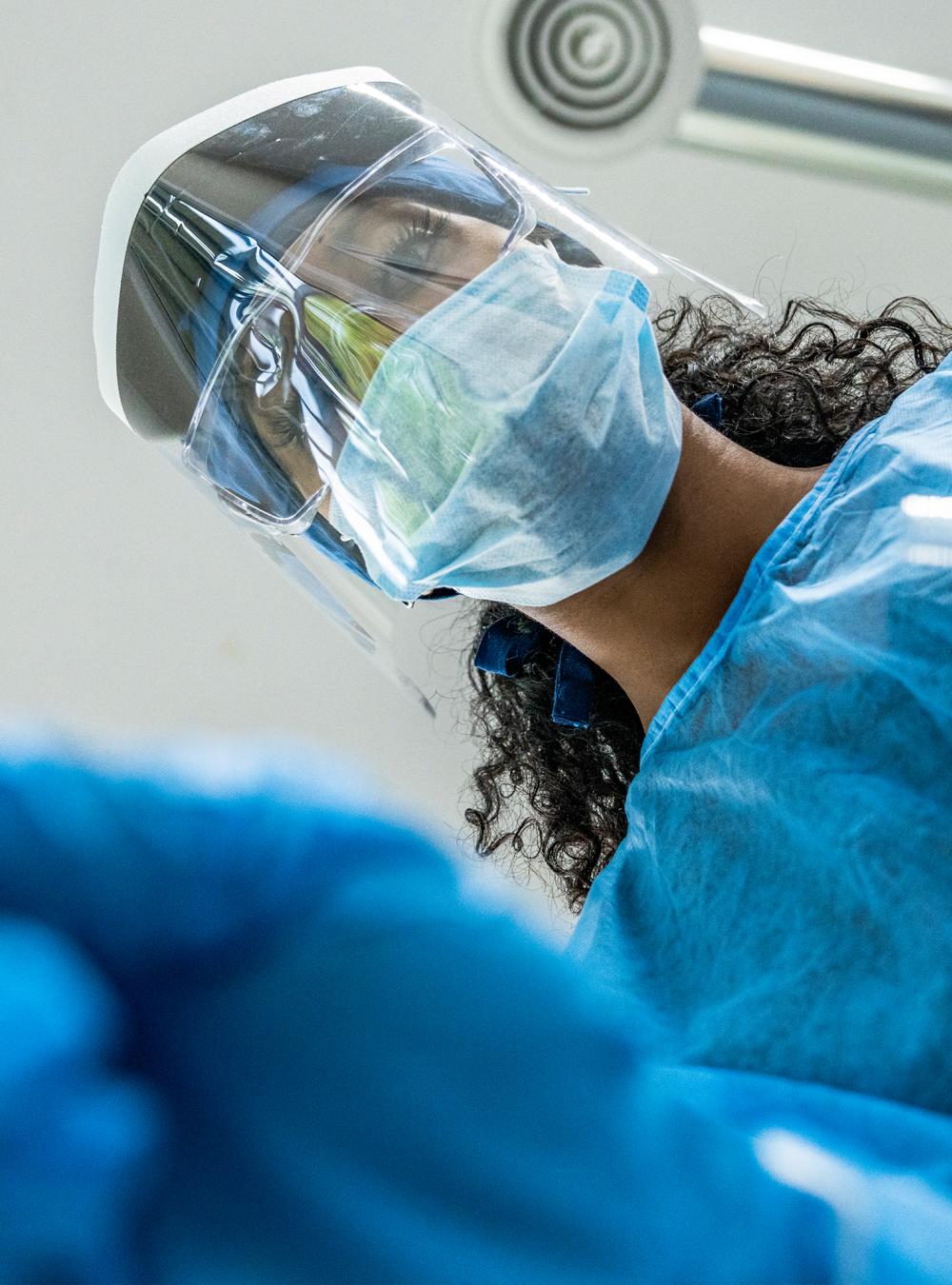
3D Printing Accelerates Face Shield Supply Chain at UVA
As the coronavirus pandemic escalated, healthcare providers at the University of Virginia (UVA) in Charlottesville started to face shortfalls in personal protective equipment (PPE). A lack of face shields was near the top of the list. Without them, medical personnel would be at significantly higher risk of contracting the virus than most individuals, because of their continual close contact with infected patients.
Always looking to the future, MITRE already had been working on a 3D-printed face shield before the COVID-19 PPE shortage concerns began and had reached out to the university to test the design. As a result of the prototyping efforts, we learned about the growing need for shields. We tapped our contacts across the university system and then shared the design with UVA's own fabrication lab. In just two weeks of our working together, the health center had enough face shields to protect its front-line workers.
The fact that we could address this critical need so rapidly is testament to the long-standing depth and breadth of the relationship between MITRE and UVA. Both organizations responded to the national crisis—and leveraged a little serendipity.
"Because of a series of small actions, we've had a big impact on public health," says Michael Balazs, site leader for MITRE operations in Charlottesville. Balazs also leads the nontraditional manufacturing section of the supply chain working group we've created as part of the COVID-19 Healthcare Coalition.
A Partnership to Respond to Medical Community Needs
Early into the pandemic, Terri Roberts, co-department head at MITRE's Charlottesville office, reached out to Pace Lochte, UVA's assistant vice president for economic development. Roberts wanted to discuss ways in which the two organizations could collaborate on COVID-19 issues.
"We wanted to find partners who could help us meet the needs of the medical community and their patients during this difficult time," Roberts says.
Our Charlottesville site has collaborated closely with UVA for the last decade in a variety of ways, including design projects and internships. MITRE even operates a site within the UVA health system, which is a top teaching hospital and medical school.
From that initial outreach, Roberts was introduced to a UVA doctor who had been hearing from anesthesiologists about their need for face shields.
Face shields provide a physical barrier for the user against airborne droplets of virus. They're often used in conjunction with face masks during particularly close contact with someone who's infected, such as during surgery.
A 3D-Printed Face Shield Designed for Comfort, Functionality, and Speed
As it happened, a MITRE mechanical engineer in Bedford, Massachusetts, Lilia Chan, had recently created a 3D design for a printed face shield.
That's the serendipitous part of this story. Chan usually works on mechanical design for direct sponsor work, but is currently involved in a small COVID-19 response work group exploring 3D printing. 3D printing uses a computer program to direct the build-up of successive layers of material into a desired object. It can be significantly faster than traditional manufacturing.
Chan explored the existing open-source face shield models, then worked to adapt them for comfort, functionality, and speed of production. The National Institutes of Health clinically reviewed her design in just a few weeks under a process that prioritizes designs for clinical testing based on demand, feasibility, and submission detail.
Chan, of course, was working from home. But luckily for everyone, she has her own 3D printer. She was able to work on her design and test it herself with plenty of input from her colleagues.
"This whole process has been a testament to people's ability to adapt during a crisis," Chan says. "It's so odd to be doing all this from home, but I worked with my colleagues virtually—and everyone was game to help."
Based on the group input, she added a brow guard to her design, thus ensuring the user is safe from droplets coming down from above. Likewise, she rejected foam for the brow guard in favor of a material that can be disinfected and therefore reused.
She printed out 15 versions of the updated model and delivered them to MITRE's Bedford campus, where security personnel served as her beta testing cohort.
Much-Needed Equipment Receives the Thumbs-Up
With their seal of approval, Chan sent the revised design to Nathan Gaul, a mechanical engineer in Charlottesville. He got a prototype into the hands of some anesthesiologists at UVA for their own testing.
They found the length of the shield, coupled with the lack of foam elements, provided a superior design for safety and re-usability. The doctors asked for 50 shields.
Roberts quickly connected the medical center with the School of Architecture's fabrication lab, which began mass producing the face shields for distribution.
UVA's Lochte says the UVA-MITRE collaboration has helped protect the health of the community in a time of true crisis.
"Challenges like these cannot be solved alone," she says. "We are grateful to have an innovative, team-focused, results-oriented partner in MITRE."
—by Twig Mowatt